How do homemakers’ work differ based on how much money their husbands earn? In what ways must their work be the same? Let’s begin with the definition of a “good provider,” referring to husbands. Often people call a man a “good provider” as a codeword for that he makes a lot of money. But, I don’t think that is only how we should define a “good” provider.
Any man can be a good provider if he has a vision for his livelihood and he is hard working. A pig farmer who has a plan that he wants to always be a pig farmer and in his vision that will likely not make ever more than a few thousand dollars a month is not a bad provider. He is providing a stable, beautiful vision for his family and work.
“Stable” does not mean a man in sales isn’t a good provider because one month he makes x and another month he makes 2x. He as well is the right kind of stable and predictable as a provider if he has a vision for his career and isn’t lazy.
No women should speak poorly to other people about the amount her husband provides her.
It is important for homemakers to acknowledge that upperclass, working class, and middle class housewives have different experiences. All can be faithful, home oriented wives.
Upper class women should not lose their vision for being centered around the home because they have freedom to hire out certain tasks. A working class wife should not abandon being a homemaker all together because she needs more money. Middle class women have some experiences of both groups.
No class of women should give in to any forms of 1) envy or 2) boredom.
How can each class be faithful and home oriented?
This rest of this post is for paid subscribers only; you can become one here.
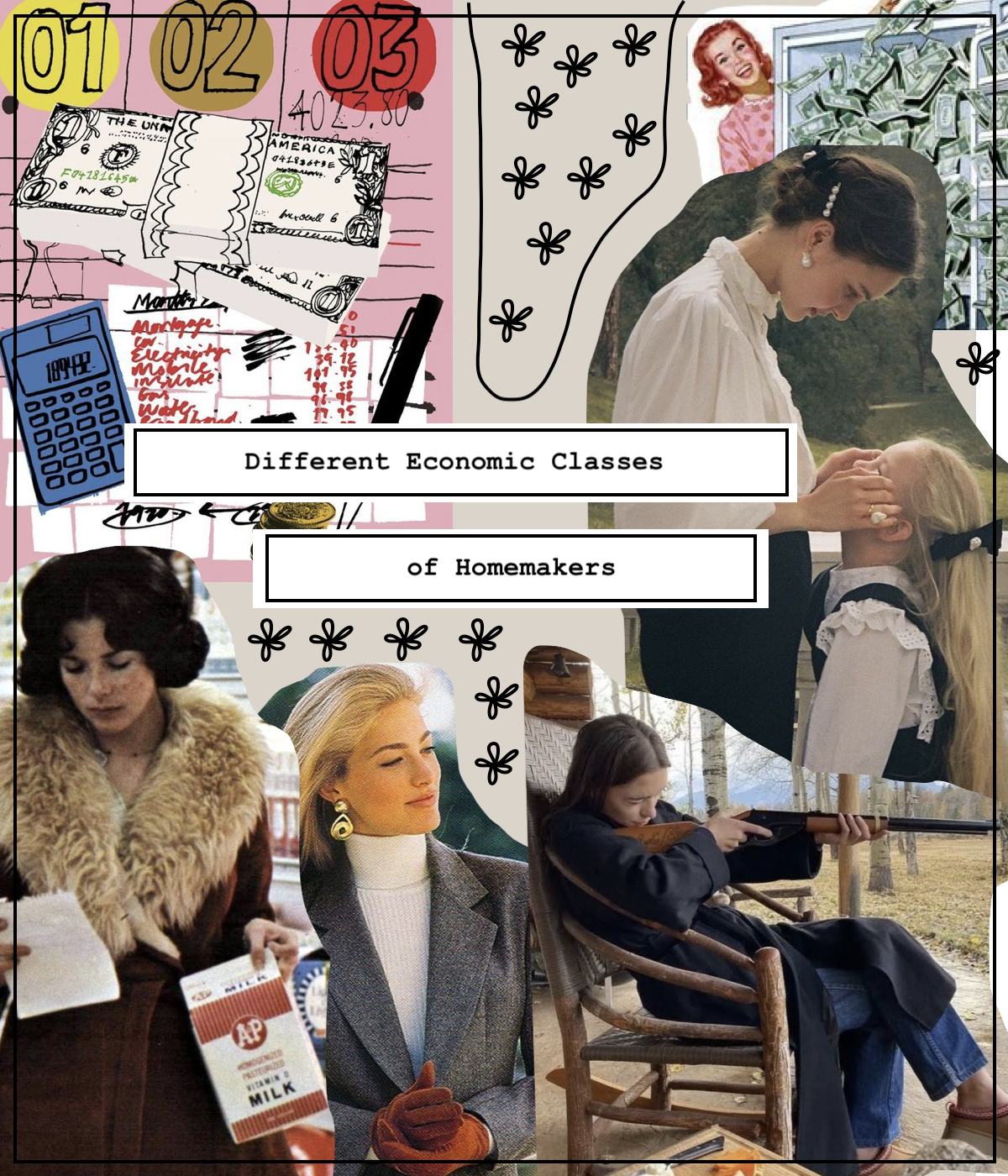
How do homemakers’ work differ based on how much money their husbands earn? In what ways must their work be the same? Let’s begin with the definition of a “good provider,” referring to husbands. Often people call a man a “good provider” as a codeword for that he makes a lot of money.